Aluminum Deck Railing Manufacturers
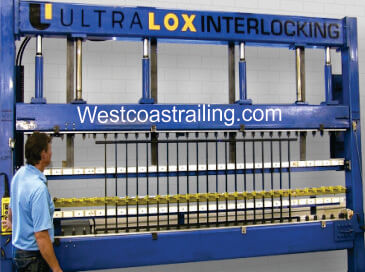
Custom manufacturer of extruded aluminum railings with secondary machining available. In-house die making capabilities to maintain quality control. Also offering aluminum extrusions in standard shapes and sizes including flat bars, rounds, tubing, channels, beams, and angles. Additional services include cutting to standard lengths, metal finishing including anodizing and powder coating, tumbling, debarring, ink jet stenciling of coding and traceability, and drilling
OVERALL DIMENSIONS
System height: 42″ minimum from mounting surface to top of rail per IBC Code, 36″ minimum from mounting surface to top of rail per IRC Code. Post heights subject to desired aesthetics.Railing spans: Limiting span variables may be subject to specific project details.
Base footprint: Determined by desired aesthetics/condition specifics.
2″ post base: 4″ x 4″
3″ post base: 5″ x 5″
MATERIALS
Aluminum
Posts: Aluminum 6005A-T5
Rails: Aluminum 6063-T6
Fittings: 5052-H32 Baseplate:
A369 Cast Aluminum Fasteners:
Stainless Steel 300 series
STRUCTURAL PERFORMANCE
Railings to be in accordance with AC273 and supporting documents as described:
Infill:
Horizontal concentrated load of 50 Ibf. applied with 2.5X safety factor for rigid substrates, 3X safety factor for flexible substrates, to 1 sq. ft. at any point in system, including panels, intermediate rails, balusters, or other elements composing infill area. Load on infill area need not be assumed to act concurrently with loads on top rails.
Uniform load of 50 Ib/ft. applied horizontally and vertically.
-2.5X safety factor for rigid substrates, 3X safety factor for flexible substrates.
Concentrated load of 200 Ib/lf. applied horizontally and vertically at midspan, adjacent to post and at top of post.
-2.5X safety factor for rigid substrates, 3X safety factor for flexible substrates.
Uniform and concentrated loads need not be assumed to act concurrently.